To make the life more colorful
PVC membrane foil, also known as PVC film or PVC sheeting, is manufactured through a process called calendaring. Calendaring is a method of creating thin, flexible sheets by passing the material through a series of heated rollers or cylinders.
Here are the general steps involved in the manufacturing process of PVC membrane foil:
PVC Mixing: The process begins with mixing polyvinyl chloride (PVC) resin with various additives, such as plasticizers, stabilizers, and pigments. These additives enhance the flexibility, durability, and color of the PVC film.
Preheating: The PVC compound is preheated to a specific temperature to make it more malleable and easier to process.
Calendering: The preheated PVC compound is then fed into a series of large, heated rollers arranged in a stack called a calender. The calender consists of several rollers, each rotating at different speeds and temperatures.
Rolling and Compression: The PVC compound passes between the rollers, which exert pressure and heat on the material. The first few rollers compress and shape the compound into a thin sheet, while the subsequent rollers further refine its thickness and smoothness.
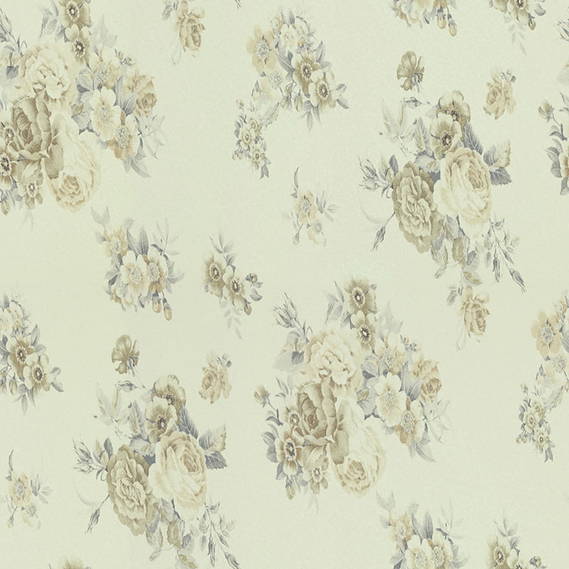
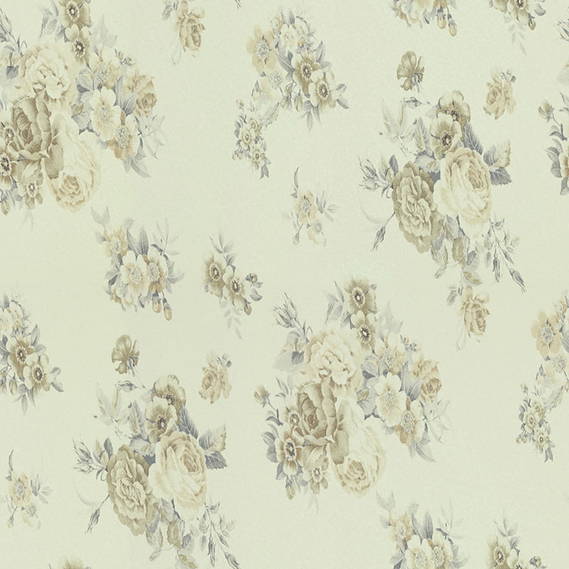
Cooling: After passing through the calendering rollers, the PVC sheet is rapidly cooled to room temperature. This cooling process is typically achieved by passing the sheet over chilled cylinders or through a cooling chamber.
Trimming and Inspection: The cooled PVC sheet is trimmed to the desired width and length. It undergoes a visual inspection to ensure that it meets the required quality standards, checking for any surface imperfections or defects.
Winding or Cutting: The PVC sheet can be wound into large rolls if it is intended for roll stock or further processing. Alternatively, it can be cut into smaller sheets or rolls, depending on the intended application and customer requirements.
Packaging and Storage: The final PVC membrane foil is packaged and labeled, ready for shipment or storage. It is important to store PVC film in a controlled environment to prevent exposure to excessive heat, sunlight, or moisture, which could affect its properties.